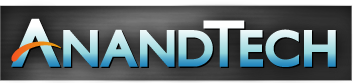
Original Link: https://www.anandtech.com/show/1350
The Birth of an Abit NF7 - A Factory Tour
by Kristopher Kubicki on June 11, 2004 10:12 PM EST- Posted in
- Motherboards
Introduction
Last year, we took the opportunity to travel with EliteGroup (ECS) and take an in-depth tour of their production facilities. On that tour, we had the chance to see PCB and motherboard assembly, as well as system building and testing. After receiving such warm response from that article, we jumped all over the opportunity to visit Abit's Chinese production facilities.Although motherboards in and of themselves are quite fascinating, the underlying political struggle between China and Taiwan lays the framework for a more interesting modern issue. As we mentioned in last year's ECS factory tour, political indifference between Taiwanese and Chinese governments prohibit Taiwanese companies from investing large amounts of money into Chinese assests; this includes factories, warehouses, etc. Traditionally, companies like Abit simply incorporate the factory as a completely autonomous corporation. Abit uses the corporation, ANCO (now ANCO-Rolly), to outsource production of their motherboards. Even though ANCO-Rolly is a separate corporate entity, they can best be described as Abit's near exclusive business partner for production. Corporations like Rolly operate constantly in sync with Abit, selling assembled boards back to the Taiwanese company at cost. On paper, these companies are technically and completely unaffiliated with each other, but off the record, they behave together like a single conglomerate.
More recently, companies like TSMC have contested Taiwan's limitations on factories in China, but it will be some time before we see smaller companies like Abit make such leaps.
Rolly (pronounced like "Raleigh") sits across the street from ASUS' Chinese production facilities, and down the street from Canon's assembly plant in the Jiansung providence. Even though people commonly claim that these factories are located in Shanghai, they are actually about an hour west of the city in the industrial work district, called Suzhou. Like Shen Zhen, Suzhou is a special city inside China where companies like Abit and Canon are allowed to practice more capitalistic business practices not typically sanctioned in communist China.
A model of the factory
Click to enlarge.
The plant was built in 1999 with Compaq when Abit received a contract to produce components for Compaq in Southeast Asia. Rolly has 12 SMT lines, about average for a production facility of this size. Most of the practices adopted by the factory in 1999 were revolutionary at the time. Compaq, one of the most conservative and diligent OEMs at the time, worked with Abit to set up one of the most stringent QA programs in the motherboard industry. For those who follow Abit's track record closely, around late 1999/early 2000, Abit's quality in motherboards increased tremendously.
SMT
And now, the part that we have all been waiting for - the birth of an NF7. Unfortunately, the unison of science and art comes particularly unceremoniously in crates of 1000. Since Abit has no PCB production facilities, four- and six-layer motherboards are shipped from out-sourced facilities, pre-traced and pre-painted. Abit Taiwan designs the PCB and sends the schematics to an OEM factory. The factory manufactures and delivers the PCB to Rolly. For a quick primer on how the PCB is constructed, check out the primer that we gave in our ECS factory tour last year.Before walking onto the SMT lines, we are presented with a small office that controls the CAD/CAM devices on the floor. This mission control board shows when each machine was last tested, from where and when the PCB for that production came, and other process vitals.
Above is an Abit NF7 PCB as Rolly receives it. These boards have already been drilled and have passed electrical quality assurance tests at the OEM. The Rolly facility will mount components via SMT, manual labor and then package the board at this facility.
SMT is a term used frequently in any sort of electrical assembly. It stands for "surface-mount technology". As motherboard speed increases, their feature set and complexity increases even faster, although disproportionately . Motherboards like the NF7 have upwards of several thousand integrated circuits (ICs) under a millimeter in length, soldered onto the traces of the motherboard. Although labor is cheap in China, such precision and finesse are required to place delicately the thousands of resistors, ceramic capacitors and other integrated circuits (SMDs) that only a preprogrammed machine can accomplish. Below, you can see one of Abit's two-years-old SMT machines placing components on the NF7 PCB.
A colleague of mine recently described SMT as "a high-powered machine gun spitting ICs onto a board with insane precision." There really is not a more accurate description. Since SMDs are stamped onto the board at such high speeds, they are loaded into the SMT machine using a special tape feeder. This is very similar to the manner in which ammunition is fed into a machine gun. Below is a quick video sample of how the entire process looks in real time.
SMT QA
After the SMT process, we can see the transformation that the board has undergone. The north and south bridges are now present, along with thousands of ceramic capacitors and LEDs. This particular board is a K8V Pro, but we would see a very similar end result on the NF7. SMT lines run the same model and do not skip around; we shot this picture from a different line.Since SMT is the most complicated procedure when producing a motherboard, rigorous testing is done at this point. The boards must past visual inspection to assure no stray SMDs are printed, and then the boards are checked to make sure every SMD is lined up properly. A single offset capacitor can mean the difference between a working and non-working motherboard.
Because of the stringent quality control, the first visual inspection is done with an overlay to help a factory worker inspect the components. You can see this process below. The inspector in this image is looking specifically for misaligned components.
Manual visual inspection is starting to get too costly and inefficient for Abit's means. The important thing to consider about labor in China is that it is very cheap; manual labor is almost always preferred when possible. On some production lines, a $200,000 visual inspection machine replaces the job of two physical inspectors. The machine and a technician can do a more exhaustive examination of a motherboard at a slightly faster pace than 1 traditional visual inspector, but the cost benefit ratio is not very good. The machine technician and the traditional visual inspectors are paid about the same; usually around $100 per month with lodging.
Several attendees on the tour were surprised about the sheer amount of physical labor in a factory like Rolly. Rolly is actually quite small in comparison to some of the other factories that we have seen. It employs 1,400 workers and runs a single 8AM to 5PM shift. Even if it takes 10 workers to do the job of a single $200,000 machine, the cost of the machine usually outweighs the cost of using manual labor. Futuristic, all machine-run factories don't exist in China.
One thing that caught our attention at the Abit factory was the process of quality control. We recall the Elite Group factory tour from a year ago; when workers detected component failure or issues with a board after SMT, the board was completely pitched. At Rolly, we noticed that if a motherboard failed, it was immediately retested. Occasionally, these boards would fail continually, but after several tries, the components would usually pass inspection. Abit representatives explained to us that this procedure was because Rolly purposely sets inspection tolerances too tight and compensates for the extra manpower to test and retest (and retest again) by relying on its relatively cheap workforce.
Assembly
On average, 1.4 out of 100 motherboards fail Rolly's quality assurance standards. These boards never leave the factory, but the cost of the components and manpower put into the motherboard are lost and translated onto the retail price. Efficiency of 98.6% is about average for a factory of this size. Although, Abit told us in the next several months that they are increasing funding to several projects,which should get this number closer to 99%. About 150 of the factory's 1400 employees are allocated solely to quality assurance testing.Above, you can see a specialized machine electrically testing the newly stamped SMDs on the motherboard. It is assumed that the PCB from the OEM is working correctly, so this is the first electrical test in the assembly process. Unfortunately, this poor NF7 does not pass inspection, even after several tries. The inspector places this board in a separate bin and it is sent to a reworking station where it undergoes manual electrical testing under oscilliscopes. The much higher skilled workers who test individual components with scopes are trained to solder or strip down a board depending on whether or not it can be reworked. Only after this stage does a bad motherboard get completely pitched. A short clip of an engineer testing a defunct board can be viewed below.
After successfully passing the first visual and electrical inspection tests, the half completed motherboard moves down to the epoch of manual labor - the assembly line. Here, 30 to 40 workers sit on the assembly line and plug components too large for SMT into the motherboard. This includes components like PCI slots, DIMM slots, capacitors, audio connectors, and anything big enough to place easily with your fingers. All of these components slide into the holes predrilled into the PCB before it comes to the factory. As we mentioned in the ECS factory tour, assembly workers are primarily female. In this particular region of the world, women usually work for less and are proven to have higher concentration at tasks such as small component assembly.
Again, you can see above the amount of manual labor used to plug components into the motherboard. Every few stations or so, a worker uses a barcode scanner to scan the board into a centralized Oracle database. Each board is tracked stringently via this system, which is also connected globally. Managers in Abit's USA or Taiwan office can watch a board undergo each stage of construction in their office via the Oracle database interface. This system also provides excellent backtracking if a board is found later to have faulty components or poor assembly. The idea is to control quality with the highest standards, and then refine the process as quickly as possible so that no boards in the future are corrupted.
Solder
After going through the assembly line, the components just placed on the motherboard are only tacted in place. In order for their transformation to be complete, they must go through an industrial oven so the solder bonds correctly to the board. This is actually the second oven on the production line; the first is used right after SMT.This is actually not an ordinary oven, its a wave solder machine. Wave solder ovens run the motherboard over a molten solder bath in order to melt the fastened components onto the board. You can see a small clip below of the motherboard passing through a final phase in the device. There are two other wave solder machines at Rolly that are completely lead free. Lead free machines use similar assembly techniques, but the solder does not contain any lead (EU legislation requires all electronics imported into the union to be lead-free by 2005). The ovens on those two lines run at different temperatures and look slightly different.
After the oven, a few workers spot solder larger components, which need a little extra to hold in place. Heatsinks and stickers are also placed on the motherboard. Everything else from this point until packaging is quality assurance.
Just like the ECS Shen Zhen facility, each motherboard is completely assembled and booted up to make sure it passes the first stage of quality control. Several custom benchmarks are run, and the system stays on for about two minutes. Each worker works on two motherboards at a time, assembling one while the other is running system diagnostics. It takes less than a minute for each worker to build the entire system.
These boards are only tested once. The workers here will bin bad motherboards into a container, which goes back to the original lab with the oscilliscopes. Good motherboards continue down the line, get scanned into the Oracle database, and are then stamped "OK" to continue on to stress testing or packaging.
However, these motherboards are still not done yet. Out of each batch of 1000 motherboards, 32 are chosen randomly for environmental stress testing, plus a 168-hour burn in. A majority of the other 968 motherboards in the batch are placed into a different testing facility where they will be burned in for 24 hours. Burn in is simply the process of running a benchmark software on the system continuously for an allocated amount of time. Additionally, 10 other motherboards per model per day are selected off the final assembly line and are fully hand-assembled into a PC. Several lucky workers spend the rest of the day making sure UT2K4 (among other software) works correctly with the sampled motherboard.
Database and Video Cards
Before we get to burn in, we stopped near one of the Oracle processing stations to take a look at the output. Each individual component from the capacitors to the sockets to the SMDs are tracked via a barcode scanner in this database. From here, workers can trace the exact components used in a motherboard assembly, from where the components came and where the motherboard is going. What makes this tool even more powerful is that any Abit facility in the world is capable of viewing this same output. Compared to other production facilities that we have seen in the past, this is quite a technological feat.Also en route to the environmental testing, we caught a glimpse of Abit's VGA assembly. The PCB and GPUs come from outside the facility, but component assembly is done here at the factory in a similar manner to the motherboards elsewhere. Unknown to many people outside of the production industry, motherboard and video card PCB typically roll off the OEM assembly line coupled together, so these two video cards below were recently attached until separated using a special scoring tool.
Environment Testing
Through the tempered glass of the large environmental testing chamber, we can see a network card plugged into an Abit motherboard. This motherboard will be subjected to temperatures from 0 to 40 degrees Celsius while running a benchmark software like 3DMark. Within a few weeks, Rolly anticipates updating these testing chambers to run the same stress tests from -40 degrees Celsius to +70 degrees Celsius. This practice of environmental stress testing is a relatively new practice and only a handful of manufacturers have adopted it.This testing chamber is just under 20 degrees Celsius right now; it will climb to 40 degrees before the test is complete.
Other motherboards are selected after this procedure for other more specific quality assurance tests. These include drop and vibration tests. Fully packaged and unpackaged motherboards will be subjected to stress tests similar to rough shipping and handling in order to assure your disgruntled postman delivers the motherboard fully functional.
Research and Development
Even though most of the R&D for Abit is done in Taipei, we ventured off the beaten path a little to check out the Suzhou. R&D in this portion of Asia is typically reserved for BIOS tweaking and production techniques. When we ventured in the lab, workers were getting ready to go home for the day. However, a few diligent engineers were still behind working on Standard Operating Procedures (SOPs). SOPs are the diagrams and instructions that the workers receive at each station, which describe exactly what they should be doing and in what detail. Other functions of the R&D facility include testing and debugging processes that would take too long to send back to Taiwan.Unfortunately, that was all the time we had for the day in Suzhou. The Rolly factory was much different from the multiple campus Elitegroup facilities from last year. Abit's total volume is much less than that of ECS, but at the same time, quality control seemed much higher and more deliberate. Abit has clearly spent the better part of the last few years controlling the quality of their motherboards.
Coming up, we have more factory tours, including a first look at facilities from AOpen and Kingston!